Archive for the ‘Uncategorized’ Category
$10 Million Plant Upgrade includes Gurtler Technology


Paul Jewison, general manager of Textile Care Services (TCS) in Rochester, MN, a division of Healthcare Laundry Services Group (HLSG), recently hosted the Gurtler Industries team at their newly refurbished plant. TRSA’s monthly publication Textile Services, reviewed TCS’s plant makeover in their October issue. TCS provides high-quality textile rental services to both the healthcare and hospitality industries including commercial laundering and delivery of linen and apparel items to hospitals, nursing homes, clinics and hotels. They are proud to be the textile supplier for Rochester’s Mayo Clinic system.

Part of the makeover was a complete redo of the TCS bulk chemical room. In addition to using Gurtler chemicals throughout the plant, the Gurtler Vis-Tex UV System on all three of the new Kannegiesser tunnels. The UV Light and advanced oxidation technology allows for greater water reuse, cleaner goods and enhanced hygiene properties. The plant’s water use is down to 0.33 gallons per pound. Plus, Gurtler’s GLSS productivity monitoring system is installed in the finishing department. Jewison expects productivity standards to improve as the result of installing the GLSS technology.

Gurtler is proud to be a partner with TCS and HLSG, supplying their chemical and system needs across their facilities in mid-America.
In attendance from TCS was Paul Jewison, general manager and Forest Rouhoff, chief engineer. From Gurtler Industries were Bill Gurtler, chairman; Greg Gurtler, president; Jake Gurtler, vice president, corporate accounts; Steve Tinker, Sr. VP of R&D and Marketing; Phil Little, GLSS manager of market development; and Chuck Perry, manager of market development (not pictured).
Paul Jewison Story

Excerpted from Textile Services the May 2024 Textile Services issue on “Sustainable Cascade Powering ‘Greener’ Laundries with Innovation”
By Jack Morgan, Senior Editor
Gurtler is pleased to see that one of our valued customers, Textile Care Services (TCS), Rochester, MN, was featured in the cover story of the May issue of Textile Services, TRSA’s monthly publication. The senior editor, Jack Morgan, reached out to Paul Jewison, VP of Engineering for Healthcare Linen Services Group (HLSG), and General Manager of TCS to discuss the topic of the “Sustainable Cascade: Powering ‘Greener’ Laundries with Innovation” and how maintenance drives sustainability in his laundry.
MAINTENANCE DRIVES SUSTAINABILITY
We could “bullet point” additional initiatives, but high-profile projects isn’t the only way that companies advance sustainability and accrue the efficiency and public relations benefits that result from those actions. For Paul Jewison, general manager of Textile Care Services (TCS), Rochester, MN, a critical element of environmental friendliness centers on effective maintenance. “Here’s what I think is sustainable,” says Jewison, who’s also vice president of engineering for Healthcare Linen Services Group (HLSG), St. Charles IL. “There’s actually a couple of different components. It doesn’t automatically mean being green because one aspect of being sustainable is making sure you’re maintaining all of your equipment.”
Beyond making a strong commitment to maintenance, Jewison says that ensuring efficient and environmentally friendly laundry operations requires a culture of continuous improvement, coupled with monitoring/analysis. “We have a culture where we’re always trying to make improvements on things. Whatever equipment we have, we’re always trying to modify it and see if it gets better.” This approach benefits one’s bottom line as well as environmental quality. “Efficiency saves water; it gets you more pieces per hour. I think that a culture of innovation really distinguishes a business,” he says. “You get into a lot of plants and they’re proud of what they’re achieving on their utilities. That’s the culture you want.” Documenting performance improvements is another critical aspect of proactive plant maintenance, he adds. This includes water, natural gas and electricity use. “You’ve got to monitor utilities every day—twice a day if you can,” he says. “You may need to invest in software that’ll measure everything you have. Because if you don’t have data, you don’t know where you’re going.” Jewison relies on the GLSS system from Gurtler Industries Inc. to monitor key metrics in real time. The GLSS avoids costly proprietary hardware in order to minimize startup and maintenance costs. It’s tracking solution features a streamlined interface that can be personalized for the specific parameters that are most important for the laundry. That makes it easier for laundry managers to monitor and review data, he says.
Technological innovation offers another way to boost sustainability in a laundry setting. For example, TCS’ newly installed tunnels will have Gurtler’s Vis-Tex™ system that uses UV light and an advanced oxidation process to treat press water for improved cleanliness and stain removal. Implementing innovative resource-conservation technologies demonstrates a company’s commitment to green operations. The TCS plant’s overall water use is slightly under .5 gallons per lb. right now. But that figure will likely drop when the tunnels are fitted with Vis-Tex, he says. “You put the Vis-Tex system on, it will recover up to 50% of that water,” Jewison says. “So it’s likely we’ll probably be in the .27-.29 range when we’re done.”
Time and Laundering – How to Make the Most of It
by Steven J. Tinker“Time is money”
“Lost time is never found again.”
― Benjamin Franklin

Time is the one thing that we can never have too much of.
When it comes to laundering, Time is one of the four main factors that determine the overall level of your wash quality, along with Temperature, Mechanical Action, and Chemical Action. All four of these factors are interrelated in that they are semi-dependent on one another. For example, mechanical action is dependent on time; the longer the wash time, the more mechanical action is imparted to the goods in the wash wheel.
Chemical action is also dependent on both time and temperature. The rate of soil removal by any combination of chemical agents decreases as time increases; this is the concept of diminishing returns: the longer you wash, the more your soil removal percentages will tend to level out or maximize. Plus, chemical activity is temperature dependent. It is a basic rule in chemistry that the rate (speed, which equals time) of a chemical reaction doubles for every 10°C (18°F) increase in temperature, or conversely, the speed of the chemical reaction decreases 50% for every 10°C decrease in temperature.
In today’s modern laundry market, maximizing efficiency is a significant factor in your ability to compete. And your chemical company should be able to help you make your operation run smoothly at peak efficiency. The cost of your chemicals may only be a few percent of your overall operating cost, but the application of your chemicals can affect the other 95+ percent of your other operational costs. Wash formulas can be designed to maximize quality and minimize chemical costs by increasing wash time and temperature. But that may not be the most efficient use of resources.
The choice of the mix of your chemicals and their application can be a significant factor in your efficiency and cost. Laundering chemicals, or soil removal agents, are usually broken into four categories: alkalis (or builders), detergents (or surfactants), water and soil conditioners, and oxidizers (or bleaches). The mix and quantity of these four chemical agent types can vary depending on the soil types and levels and the textiles (cotton, polyester, or blends). Plus, the mix of your chemicals can determine the chemical cost; alkalis and bleaches are relatively low in cost per ounce, and detergent/surfactants and water/soil conditioners are fairly high in cost per ounce. Understanding all that, a well-designed wash formula can maximize your overall efficiency and minimize your overall costs.
One of the newest innovations in laundry chemical technology is the introduction of detergents with specially blended surfactants that are excellent in grease and oil removal. And with the increased use of 100% polyester textiles, alkalis can be minimized in soil removal. This high surfactant-low alkali technology and the expanded use of polyester textiles have created an opportunity to change the mix of Time, Temperature, Mechanical Action, and Chemical Action, resulting in significant savings for your operation. For instance, with reduced use of alkalis, and because there is less active chemistry to rinse out of the wash, formulas can be adjusted to eliminate at least one rinse, saving water, energy, and time. There are numerous examples in the market where this innovative technology has reduced wash formula times by as much as 25% and a similar increase in wash aisle productivity.
With these new, unique surfactant blends, oily soil removal from polyester textiles is maximized at lower temperatures than with traditional cotton textiles. Typically, the most effective temperature is 140°F rather than 160-180° temperatures used on cotton-based fabrics. Lowering temperatures and eliminating rinses saves energy and water, a big plus in your environmental stewardship program.
Other factors that can affect your overall costs and quality are your water quality, soil sortation categories, equipment, and more. But we want to focus on Time. Wash aisle productivity improvements due to shorter wash formulas may mean lower labor costs if you are operating more than one shift or more than eight hours. One facility has been able to cut wash operations from over nine hours a day to under eight hours, eliminating overtime costs. But more importantly, shorter, more efficient wash formulas can give you the capacity to grow your business by up to 25% without a capital investment in your wash aisle. That can turn into a significant increase in cash flow for your operation. That proves Ben Franklin’s adage: Time is money.
Newest Technology Can Reduce
Your Overall Processing Costs

From the traditional wash process that equally weighs the effects of of Time, Temperature, Mechanical and Chemical Action, we can transition to a new ratio of the four factors to reduce Time, Temperature, and Mechanical Action, with an increase in the ratio of Chemical Action which allows you to “shrink” your overall processing costs, saving time and money.
Dialing in Chemical Representative/Laundry Relationships

By Matt Poe, Editor, American Laundry News The April 2024 edition of American Laundry News features the article “Dialing in Chemical Representative/Laundry Relationships” by Matt Poe, Editor. The article focuses on the key factor of the successful processing of goods is relationships, and one of the most important relationships is that of the chemical representative and the laundry operator.
American Laundry News reached out to operators and chemical suppliers and communicated with five professionals on this subject. Steve Tinker, senior vice president of research and development, marketing, for Gurtler Industries Inc. was one of the contributors. Below is Steve’s response to ALN.
Q: In general, how involved should a chemical representative be in a washroom operation?
A: Good wash formula design, taking into account time, temperature, mechanical action, and chemical action requires a broad understanding of the entire laundry operation. For example, wash formulas that are focused on reducing chemical cost could be designed to make up for the lower chemical action by increasing both time and temperature. However, that could cause an unwanted increase in energy usage and a decrease in production, or pounds of clean laundry produced per hour. So, understanding all the factors that can affect the overall operation is the key responsibility of a well-qualified chemical representative.
Good chemical reps can act as a consultant that reviews your overall operation, from soil-sort to washing to final finishing, to make sure that the process is running smoothly at maximum efficiency, producing the highest possible quality at the lowest possible overall cost.
Q: How often should a rep contact and visit the laundry? Why?
A: Generally, once per month visit is recommended. And the length of a service visit can vary from 4-8 hours, however for very large operations that service call could be completed over a couple of days.
But don’t consider the time factor of a service call as a measure of the quality of a service call. Thoroughly trained, experienced chemical reps can delve into problem solving quickly and effectively, proposing a plan of action to resolve issues.
Another thought: Well-designed and engineered chemical dispensing systems with proven service life and robust performance is a key. If your rep is spending too much time testing, calibrating, and/or repairing their chemical dispensing system they may not be paying attention to the laundering operation and process to identify potential concerns, quality issues, or formulations that out of balance.
Q: Who should the rep be working with at the laundry? Why?
A: Gurtler Industries recommends that our representatives meet with the owner or general manager at the beginning of the service call to review any recent concerns that may have developed since the last service visit, and at the end of the service call to review all the actions and recommendations that we included in our service report. During the service call the rep should interact with line management or leads in each department, (such as soil sort, washroom, finishing department, maintenance, etc.) to make sure that any issues are reviewed.
Q: Should the rep be advising on formulas? Equipment? Washroom practices? Other segments of the wash aisle? Why or why not?
A: For certain the chemical rep should advise and/or develop wash formulas, however this should be a cooperative relationship with management, to make sure that the overall goals of the management team are well understood. Laundry chemical cost can be only a few percent of the overall operational costs of a laundry, however mis-applied chemicals or poorly designed wash formulas can affect the other 95+ percent of operational costs, perhaps driving water and sewer costs out of line, using too much natural gas due to unbalanced hot water use, or increased wash formula times will drive down wash aisle productivity.
Your chemical rep should be inspecting the wash equipment looking for issues, such as leaking drain valves that can cause both a quality issue and an increase in water and energy costs. He or she should also make sure the soil sort operation is designed appropriately. A new textile or garment or customer may call for a new soil sort classification and a new wash formula to maximize processing efficacy.
Q: How can a laundry operator and the rep create a solid working relationship?
A: Communication is the key. Helping the line management make sure that their goals are met, while also communicating with upper management. Previewing the goals of the service call with management and following up with action steps keeps the information flowing from month to month. I recommend developing an approach that has long-term goals. For example, perhaps management is concerned that there is too much overtime labor costs. The chemical rep can suggest changes to the operation designed to reduce labor costs, such as designing wash formulas that are 10% shorter in time, allowing for a higher throughput in the wash aisle. The chemical rep can establish goals, test new wash formulas or new chemistry and measure quality and time savings, and report the findings to management, over the course of a few months.
Q: What are some signs a rep is getting too involved? Not involved enough? How can these be addressed before the relationship is strained to the breaking point?
A: A chemical rep should only be as involved as upper management wants. Again, good, two-way communication is the key. An annual review of the service goals and results is a good way to make sure that the service provided by the chemical rep matches the expectations of the management team.
Q: Please share anything else you consider important in the chemical rep/laundry relationship.
A: A good rep will communicate new chemistry, technology, systems, and industry trends to their customers as they are developed, making sure that the customer understands the potential benefits.
Read the full story on American Landry News website:
(Excerpted from American Laundry News, Volume 50, Number 07, April 2024)
REINO LINEN/HLSG— DRIVING GROWTH IN THE MOTOR CITY HEALTHCARE MARKET
Reino Linen an HLSG facility in Brownstown, MI, is a trusted partner/customer of Gurtler Industries and was recently featured in the April issue of TRSA’s publication, Textile Services. From the article: Reino Linen uses the full range of Gurtler laundry specialty chemicals and dispensing systems on their tunnels and washer-extractors. In addition, the plant also has the Gurtler Laundry Software Solutions (GLSS) tracking program. The GLSS system facilitates real-time data collection from production equipment to assist staff in tracking productivity. In the plant, the TRSA team saw several GLSS video screens in the wash aisle displaying production/productivity numbers. The system helps employees and managers meet the plant’s productivity goals, Sean Flanders, HLSG’s VP of operations says. This data is also used in the plant’s route-accounting system from ABS Laundry Business Solutions.
Here is the full article:

Investments in people and plant are reinforcing this Detroit-area laundry’s position as a market leader
By Jack Morgan

Reino Linen Service’s plant in Brownstown, MI, has elevated the idea of continuous improvement to a fine art. Recent moves range from acquisitions of new machinery to textile testing for hygiene and boosting hourly pay to “above market” rates. These and other efforts have enabled this 92,000-square-foot (8,457-square-meter) plant southwest of Detroit to focus on “best in class” quality and efficiency.
When asked if this facility, which in 2022 joined the St. Charles, IL-based Healthcare Linen Services Group (HLSG), leverages its status as a high-quality, high-volume operator to bring in new business, Sean Flanders, HLSG’s VP of operations, north region, answers that, “I think it does, but at this particular plant, we have always emphasized quality first, growth second.
GROWTH AND CHANGE
Reino Linen’s Brownstown facility didn’t always occupy such as lofty place among area outsource-healthcare linen providers—though that was the goal from the start in 2009. That’s when co-owners Judy Reino and her late husband Leonard saw an opportunity to expand from their single-plant operation in Gibsonburg, OH, about 30 miles southeast of Toledo. Their goal was to tap into the Detroit market with a new facility in Brownstown, which is roughly the same distance from the Motor City.
Textile Services toured the new plant shortly after its opening. We published a profile article on Reino/Brownstown in March 2010 (pg. 38). The key watchword then was encapsulated in the catchphrase “Partners for Cleaner Today and a Greener Tomorrow.” That slogan still rings true today.
On our first visit to the Reino/Brownstown plant—designed by the Reinos and a consultant, the late Don Pedder—we saw a well-equipped startup. However, it didn’t have near the 45 million-48 million lbs. (20.41 mil-lion-21.7 million kg.) that the plant processes annually today. Early on, Reino/Brownstown also confronted labor challenges. The Detroit area is known for highly paid manufacturing jobs in autos and related industries. That made it difficult at first for Reino Linen to staff its facility.
Today, that’s changed as Reino/Brownstown—like other laundries facing labor shortages—has upped wages to assist with staff recruitment/retention. “We chose to kind of get above the market,” Flanders says, noting that higher pay has helped Reino Linen compete not just with fast-food outlets but also high-powered competitors like Amazon. During the COVID-19 pandemic, the online retail giant hired away several Reino production employees, but pay hikes implemented last year have helped Reino retain staff. “There were two large Amazon warehouses locally, and they were just gob-bling people up,” Flanders says. The labor shortage has leveled out now. As for route staff, Reino has had better luck keeping its team of drivers intact, despite robust demand for delivery drivers from Amazon and other large companies. “We have some pretty long-term drivers here and that retention has been really good,” he says. “We’ve been pretty blessed there.”
Another bit of good fortune is the fact that healthcare spending in the U.S. has grown exponentially in recent years. According to websites citing U.S. government data, in 1970 healthcare spending stood at $74.1 billion. By 2000 that figure had mushroomed to $1.4 trillion.
By 2022, speeding had jumped again to $4.5 trillion. Spending per capita for healthcare rose from $353 in 1970 to $13,493 in 2022 (in constant 2022 dol-lars). Today, the rate of healthcare spending shows no sign of slowing, as aging baby boomers and population growth continue to drive demand for services. The pandemic that began in March 2020 also fueled a spike in healthcare spending, according to statistics cited in www.healthsystemtracker.org. From 2019-2020 health spending rose by 10.6%. In the next two years, growth in health spending mirrored that of the 2010s at 4.8%.
While the healthcare “pie” is growing, that’s no guarantee for a laundry operator like Reino Linen, unless they can deliver on the demands of client hospitals and outpatient centers. That takes investments, not only in staff, but also in machinery and systems to expand capacity, while improving efficiency.
We learned more about the Reino/Brownstown plant during a walk-through of this two-shift facility.
IN THE PLANT
The Reino/Brownstown plant is located in a suburban industrial park. It opened in a building that was refurbished for use as a healthcare laundry. The owners were lucky to find a structure of sufficient size that had the water, sewer and electrical hookups necessary for a high-volume operation in a location with ready access to area highways. Soiled goods enter at the back of the building through a series of loading docks. Trucks bring in flat-work and garments from eight hospital and four clinic routes. Each cart is barcoded, and each load of soiled items are scanned and weighed so that the laundry can track them—including customer-owned goods (COG) and rental items—throughout the process.
BELOW: (Clockwise from top/left) A view of the one of the plant’s two tunnel washers; water-softening equipment and storage tanks in the mechanical room; clean-side rail operations; a view of chemical-injection equipment between the two tunnels; on the opening page: an overview of two flatwork ironer lines.

The staff process customers’ COG items separately from the rental goods. While COG is common in hospitality plants, healthcare laundries typically lean toward rental. In that sense, The Reino/Brownstown situation is unusual. “We are, to my knowledge, the largest mixed healthcare plant in the country because most of the large plants, including our own Logan’s Healthcare plant (Shelbyville, KY) are all rental. We’re actually kind of 60-40 COG.” Having a large quantity of COG textiles adds to the complexity of ensuring quality and service. “That’s what makes it tricky is there are a lot of changes in a large plant that was set up for rental automation,” Flanders says. When the plant opened, the owners may have thought they could convert COG accounts to rental. These COG customers apparently prefer owning their own textiles.
The next steps in processing are sorting and washing. Employees roll carts to a Kannegiesser/ETECH cart dumper that lifts the cart so that plastic bags filled with soiled items drop onto a table. Employees tear open the bags, remove any waste items and send the goods on a conveyor for sorting. Isolation gowns and other garments are fitted with radio frequency identification (RFID) tags. These are read as the goods pass under a metal hood fitted with an RFID antennae. Both the tags and related equipment are from Positek RFID. The plastic waste from the bags is compressed in a compactor for recycling.
After sorting, the COG and rental goods go into sling carts. When fully loaded and weighed, the slings are raised on a hoist to a storage area in the ceiling. The plant has 16 Kannegiesser ETECH storage rails that can accommodate up to 200 slings of soiled goods. A computer dispatches the slings to one of the two Kannegiesser tunnel washers once space is available. One tunnel dates to the plant’s opening. It has 14, 187 lb. (85 kg.) modules. A second tunnel, added in 2016, has 16 modules of the same size. The tunnels, as well as the plant’s conventional washers, use laundry chemicals from Gurtler Industries Inc. The plant also has the Gurtler Laundry Software Solutions (GLSS) tracking program. The GLSS system facilitates real-time data collection from production equipment to assist staff in tracking productivity. We saw several GLSS video screens in the wash aisle displaying production/productivity numbers. The system helps employees and managers meet the plant’s productivity goals, Flanders says. This data is also used in the plant’s route-accounting system from ABS Laundry Business Solutions. After processing in the tunnel, goods move to the press to remove excess water. Clean, pressed “cakes” then emerge and move via conveyor to any of 32, 187 lb. (85 kg.) dryers.
The plant has a large conventional wash aisle as well. This area is used mainly for small lots and stain-rewash items. Machinery here includes 10 washer/extractors, ranging in size from 30 lbs.-100 lbs. (13.6 kg.-45 kg.) There are also 11 pony dryers, ranging in size from 50 lbs. to 170 lbs. (22.6 kg.-77 kg.). Plant staff have recently undertaken an initiative with stain-rewash efforts in order to reclaim more linen for customers, Flanders says.
As we move toward the clean side of the plant, we stop off in the mechanical room. Here we see two 400 HP boilers, plus an 11,000 gallons-per-day boiler make-up system and boiler feed pumps. There’s also a 1,500-kw generator that can power the plant in case of electricity outages. We see an energy-saving heat exchanger from Kemco Systems Inc., as well. Overall water use is 1.2 gallons per lb.; in the tunnels it’s .8 gallons per lb. Other equipment here includes water-softening tanks, air compressors and a shaker screen for removing lint from wastewater.
Controlling lint from the wash aisle and finishing operations poses a challenge for any linen processor, and Reino/Brownstown is no exception. “These large plants produce lint all day long,” Flanders says. The plant recently acquired several portable fans from Sonic Aire Inc. The fans are placed on long poles that staff can deploy as needed to blow lint down from surfaces, so maintenance staff can sweep it up and remove it. Apparently, the systems are working. We saw very little lint in this plant.
Moving to the finishing area, we notice a walled separation between the clean and soiled areas of the plant. This helps prevent airborne microorganisms from moving to the clean side. The plant also has negative air floor from clean to soil. Ensuring control of microorganisms on textiles is a critical issue for customers, particularly after the COVID-19 pandemic. To that end, Reino/Brownstown coordinates with Gurtler to conduct additional testing on linens by an outside lab. “We have not failed a single one yet,” Flanders says of the tests, which help reassure customers on the laundry’s antimicrobial protocols.
The plant’s finishing area is a hub of activity. Here we see a Kannegiesser ETECH clean-side rail system that moves goods from sling carts filled with textiles from the dryers. A hoist lifts them to a 12-rail storage area that can accommodate up to 200 slings for the next stage of processing. The plant has seven ironer lines, including three Kannegiesser 2-roll machines, three JENSEN 3-role machines and one 6-roll Hypro ironer from American Laundry Machinery Co. The JENSEN and Kannegiesser ironers are each equipped with feeders and folder/stacker equipment. We also see 10 small-piece folders: six from Kannegiesser and four from JENSEN—plus two garment folders from Kannegiesser. RFID tagged gowns, scrubs and other items are counted in bulk in a Positek scanning shed in the packout area.
We stopped briefly at the plant’s operating room (OR) pack area as well. Here, employees assemble OR towels drapes and other goods for use in OR packs. While Flanders says disposable OR goods still predominate at area hospitals, the Reino/Brownstown staff assemble 500-1,000 reusable OR packs a day.
Other equipment in the finishing department includes a Rennco bagger for towels and other small pieces, a Kannegiesser tunnel finisher for garments, a G.A. Braun Inc. folder and a Felins heat tunnel for shrink wrapping plastic-covered stacks of finished textiles. As goods emerge from these systems, employees inspect these goods and place them on carts for movement by truck to the plant’s hospital customers, including 350 outpatient centers affiliated with the hospitals.
In the finishing department and in all areas of the plant, Reino/Brownstown staff take a proactive approach to safety. When we asked Flanders about the safe-ty program, he answers that it’s easier to “show you” because safety at Reino/Brownstown is mostly about awareness. We saw evidence of that commitment in large signs posted around the plant that read “Safety Starts With You.” Others featured photos of company employees with a tagline below, saying “I am Safety.” But the safety effort here goes beyond slogans. Reino/Brownstown has an active employee-driven safety committee that’s overseen by a full-time safety executive at the corporate level. Michelle McNeil, who serves as director of safety for HLSG, regularly visits Reino Linen and the group’s other 19 plants, which process a total of nearly 350 million lbs. (158 million kg.) annually. Plant managers are also active in the program. “We have our Safety Committee members, and our management team attends those meetings,” Flanders says. He adds that employees can call for impromptu meetings anytime they have a safety concern. This hands-on approach—from hourly staff, plus plant and corporate management—enhances the safety program’s effectiveness, Flanders says.
BELOW: Pressing equipment in the finishing area; Reino Linen leadership team: (l/r) Brian Milano, director of transportation; Sami Harrison, HLSG corporate trainer; Matt Doss, Brownstown plan manager; Sean Flanders, HLSG vice president of operations, north region; and Dennis Taucher, Brownstown chief engineer.

CLEAN HANDOFF
Seeing today’s Reino Linen/Brownstown leaves no doubt that the growth that seemed improbable in 2009, has now come to fruition, thus fulfilling the vision of its founders. Now, having completed an ownership transition to HLSG in 2022, what’s next for Reino Linen? Flanders points to additional investments in equipment, such as a pending deal for two new Olma folders from J.P. Equipment Inc., that will help meet a growing demand. Meanwhile, the healthcare textile market post-COVID has shifted in ways that bode well for Reino Linen’s role as a leading launderer for the Detroit-area healthcare market. Specifically. Flanders cites an expansion of textile vendors offering competitively priced quality goods that are helping Reino Linen control costs. “The HLSG Reino/Brownstown Laundry has experienced additional opportunities to purchase linen items as a multitude of smaller linen manufacturers have entered the marketplace, allowing better cost initiatives and savings opportunities,” he says. A third positive development is the prospect of converting more hospitals in this market to reusable isolation gowns. “Reusable gowns are a priority linen item and are being used more frequently after the COVID pandemic,” he says. “There are still some facilities that utilize disposables, but long-term plans call for the discontinuation of said items.” Reusable iso gown use during COVID peaked at 35,000 per day. It’s now at 15,000-20,000 per day, but has “held steady,” Flanders says. Fourth, while inflation has taken its toll on Reino Linen’s bottom line, utility costs recently have stabilized, he says.
While Reino Linen/Brownstown could face new challenges going forward, its bold focus on continuous improvement—from equipment to labor relations—and its commitment to quality, service, hygiene and safety for its customers and nearly 200 employees, bodes well for the future. Bottom line? To us, it looks as though this plant will continue to lead the Detroit-area healthcare textile market for years to come.
JACK MORGAN is senior editor of Textile Services. Contact him at 540.613.5070 or jmorgan@trsa.org.
Gurtler SOLS Customer Testimonial
Southern Oregon Linen Services: “The VisTex UV innovations have helped lower our plant’s water usage rate to an average of .52 gallons per lb.”

Long-time Industry Professional Andy Feldman Joins Gurtler Industries
Gurtler Industries is pleased to announce that Andy Feldman has accepted an expanded role with Gurtler Industries. In this role, Andy will be responsible for enhancing Gurtler’s company-wide sales growth. He will be leading Gurtler’s sales efforts by supporting and coaching Gurtler’s outside personnel through all stages of the sales process up to and through post-installation. Additionally, he will be charged with helping create, implement, and lead Gurtler’s marketing programs beginning in 2024 including augmenting Gurtler’s presence at industry events. Further, he will be tasked with managing existing customer relationships in which he has cultivated a long-term partnership. Lastly, Andy will continue to support the assimilation of the Vis-Tex Tunnel UV Systems acquired earlier this year including harnessing the full innovation potential of this innovative technology.

Gurtler acquired the Vis-Tex Tunnel UV technology for commercial laundries from OMNI Solutions in March 2023, when Andy joined Gurtler on a consultant basis. Greg Gurtler, president of Gurtler Industries commented, “I have known Andy for almost 30 years. He is the fourth generation of his family to work in the commercial laundry industry and his family still owns and operates laundries. During his three decades in the industry, besides working production and running laundries, Andy has been a vendor for both chain and independent laundries nationwide.” In the industry, Andy has served as the chair of the Textile Rental Services Association (TRSA) sales and marketing committee and has been a contributor to TRSA’s Textile Services magazine. In addition, Andy has taught classes at TRSA’s Professional Management Institute (PMI) and Executive Management Institute (EMI) and led training with CSCNetwork and the Association for Linen Management (ALM).
Most recently, Andy helped grow OMNI Solutions from a small OPL provider into a multi-million-dollar business. Andy is also a professional sales trainer and coach and has worked with many companies, including AFLAC, T-Mobile, the US Army, Capital One, Lincoln Financial, and the NY Mets.
Andy has spent the past eight plus months learning the Gurtler way and spent considerable time in the field with many members of the Gurtler team. Andy says, “After interacting with Gurtler’s management and their sales and service team, I learned of Gurtler’s commitment to service, quality, innovation and personal training and development of employees. These factors made my decision to join Gurtler very easy.”
Greg continues to say, “I believe Andy’s experience and expertise will assist Gurtler in further establishing our company as the leading chemical supplier to commercial laundries across North America.”
Gurtler Industries is a leading manufacturer of advanced detergents, specialty chemicals and injection systems for the commercial laundry industry. From its headquarters and research center in suburban Chicago, Gurtler supports the entire spectrum of the laundry industry, including healthcare, hospitality, industrial uniforms, shirt laundries and textile rentals. Gurtler is a family company now in its third generation, maintaining its tradition of excellence, innovation, and service.
For more information, contact Gurtler Industries at 1-800-638-7300, or contact Steven J. Tinker at 708-331-2550, or at sjtinker@gurtler.com.
Gurtler Congratulates Wildman on their Acquisition of WM Uniform

Wildman Business Group based out of Warsaw, Indiana recently announced the acquisition of and partnership with WM Uniform of Holland, Michigan. In their announcement, Wildman observed that as another independent, family-owned business with shared values, they are honored that WM Uniform chose Wildman as their partner to continue their family’s legacy in quality customer experience and exceptional team member care. For the most seamless customer experience, both companies will retain their independent names and individual branding – and continue to serve customers with the same sales and service teams.
Gurtler is proud to be a trusted partner with both Wildman and WM Uniform. Founded in 1952, Wildman has been providing industrial laundry, uniform and rental services throughout the state of Indiana and beyond. WM Uniform is in their 3rd generation of ownership and services a large part of Michigan, providing uniform rental services, mat and towel rental and restroom products, plus custom logo apparel programs.
Wildman, as a family-run business, has grown substantially, as three generations have been involved with the success of Wildman Uniform. Gurtler has been a valuable partner to Wildman in this highly competitive market. Like Gurtler, Wildman relies on their knowledge and expertise to keep ahead of the competition. “Helping Wildman find ways to conserve energy, save water and still produce top quality garments will not only help them grow in the future – but benefit Gurtler as well,” says Greg Gurtler, President of Gurtler Industries.
Wildman’s CEO, Josh Wildman, says of Gurtler, “Doing business with another family-owned company that shares our values and commitment to customer relationships and excellence in service and products has been the perfect partnership for Wildman. We have remained not only business partners for over 20 years, but we consider Gurtler part of our family.”
Drew Scholl, Wildman’s VP of Operations says, “Gurtler’s innovative Work•Clean Team chemical program has enhanced our cleanliness and quality of finish, while delivering reduced costs in water and energy, improved wash turn time, and increased productivity.”
Steven Van Tuinen, VP of Operations for WM Uniform has also expressed his appreciation of Gurtler’s service, innovation and people: “Gurtler is a trusted partner with WM Uniform. Doing business with another family-run and operated business that shares our values and understands our challenges is a big plus. Their commitment to quality service and innovative technology helps WM Uniform excel. Gurtler’s Work•Clean Team of products has reduced our wash formula run times, improving productivity, saved water and energy, all while maintaining our high quality standards. There is no better partner!”
Gurtler congratulates both Wildman and WM Uniform on their partnership and commits to work with them to continue their record of success.
STRONGER TOGETHER— NEW BOARD MEMBERS: GIVING AND GROWING WITH TRSA & THE INDUSTRY
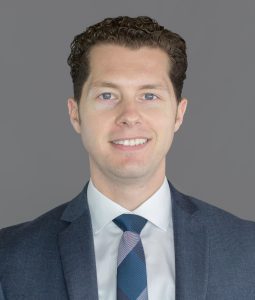
By Jack Morgan, Senior Editor, Textile Services
As part of its regular rotation last September, six new members of TRSA’s Board of Directors were elected during the association’s Annual Conference in Nashville, TN. The reasons they cite for taking time out from their busy lives to lead the association include a desire to give back, while strengthening the linen, uniform and facility services industry.
One of the six members is Jake Gurtler, vice president of corporate accounts of Gurtler Industries, a third-generation leader of this laundry chemical supplier that serves customers across North America, the Caribbean and Australia. Gurtler started in the industry in 2008 after graduating from Calvin College, Grand Rapids, MI. He began as a Midwest sales rep. and has worked his way up in the company that his grandfather Bill founded in 1982. Jake’s father Greg leads the company today as president of Gurtler Industries Inc. Jake currently co-chairs TRSA’s Next Generation Executives Network (NGE) and has completed TRSA’s Professional Management Institute (PMI) and the Executive Management Institute (EMI). His service on the TRSA Board is a step forward in his career development, as well as an opportunity to give back to the industry that’s fueled his success. “It is an honor to be called to service on the board,” he says. “I am passionate about our industry, and I want to do my part to ensure its success for future generations. As an association, TRSA has provided me with countless opportunities to learn, grow, network and form many excellent friendships. I encourage anyone interested to attend a meeting, join a webinar, sit in on a committee meeting, attend a PMI/MMI (Maintenance Management Institute)/EMI course. Get involved, and you will quickly see the impact that this association makes in strengthening our industry.”
(Excerpted from Textile Services, Volume 106, Issue 7, March 2023)
2022 TRSA Above and Beyond Service Award Nomination – Nicolas Legault
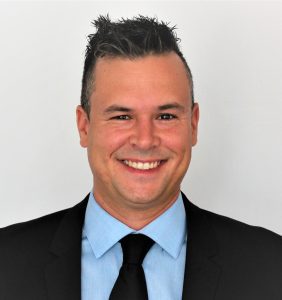
Nicolas Legault is the Regional Director of Gurtler’s Canadian business unit, based out of Montreal, Quebec. In addition to managing our Canadian sales team he has one of Gurtler’s largest sales territories that he personally services. Gurtler surveys our customers annually as part of our ISO certification program. In 2022 Nicolas’ customer ratings were a consistent 5 out of 5 for his quality of service, response time for problem solving, and his technical support. Nicolas received a “perfect” score, 120 out of a possible 120 points from his customer ratings. At the recent Gurtler Global Sales Meeting Nicolas was recognized by Gurtler as the 2021 Salesperson of the Year for his excellence in customer satisfaction, customer retention and sales volume and growth.
One of Nicolas’ customers, David Diachidos, chief of laundry and linen services at Jewish General Hospital, Montreal, Quebec has the following comments: “It is important to me that you know how satisfied I am with the service we receive from Gurtler. Everyone we deal with is kind and helpful, extremely responsive. I would particularly like to highlight the quality service we receive from Nicolas. He always makes time to talk to us and explain all about the industry. It is always a pleasure dealing with him and everyone on the team. Please keep up the great work!”
Chad Laframboise, general manager of Northern Uniform, Sudbury, Ontario, also comments about Nicolas: “In my 16 years in this industry I have never encountered another individual with his work ethic and deep concern for customer well-being. Every action is deliberately planned, satisfying today’s needs while positioning wisely for the future. His contributions far outreach his responsibilities; he is not just a vendor rep, Nicolas is a part of our team, a true friend of Northern Uniform. I would go so far as to say that we have a competitive advantage in the marketplace with Nicolas on our side.”